CO2をほとんど排出しない「常圧スマート浸炭」とは?
- 浸炭処理
- ダイレクト浸炭
2024/10/19
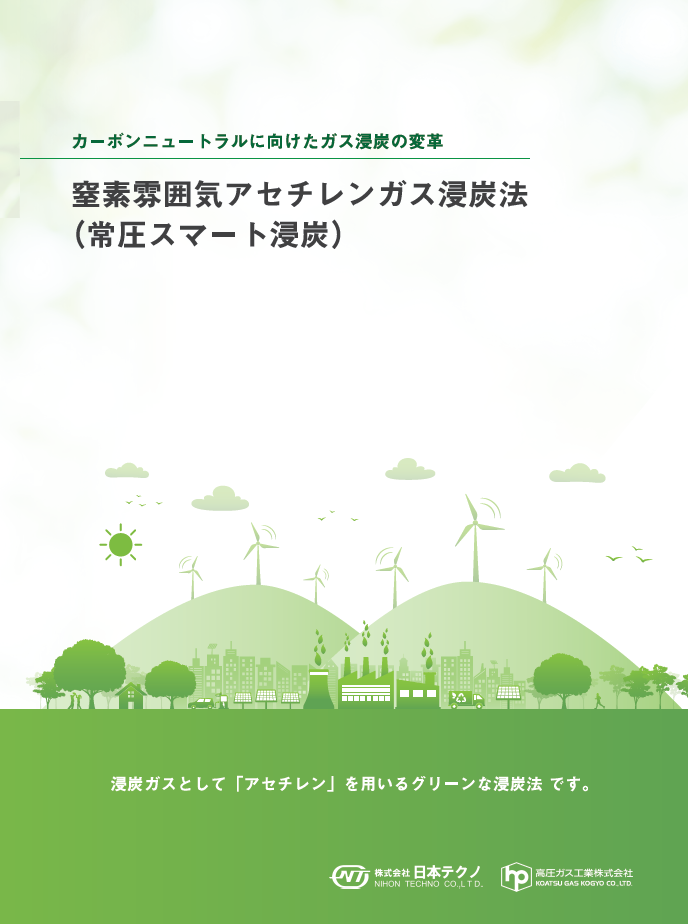
常圧スマート浸炭は、環境に優しい革新的な浸炭技術で、従来のガス浸炭法と比べてCO2排出量を大幅に削減できる点が大きな特徴です。この技術は、日本テクノと高圧ガス工業が8年以上にわたり共同開発し、アセチレンガスを直接使用することで、変成炉を使用せず、短時間で効率的な浸炭処理を実現しています。特に、カーボンニュートラルを目指す企業にとって最適な技術であり、さらにエネルギーコストの削減と生産性向上、作業環境の改善にも大きく寄与します。
本記事では、浸炭焼入れの概要から、従来のガス浸炭の課題、常圧スマート浸炭の原理、特徴、そして日本テクノだからこそ可能な常圧スマート浸炭の特徴から、実際に行っている試作開発事例まで、詳しく解説します。脱炭素化が進む現代の製造業における、新しい熱処理技術「常圧スマート浸炭」の可能性をお伝えします。
浸炭焼入れとは?
浸炭焼入れは、鉄鋼材料の表面に炭素を浸透させることで硬化させる熱処理法です。この技術は、自動車部品や産業機械の耐摩耗性や耐久性が求められる部品に広く利用されています。浸炭焼入れの主な目的は、部品の表面を硬くしつつ、内部は靭性を保つことで、全体の耐久性を向上させることです。機械部品が外部からの衝撃や摩耗に耐え、長寿命で使用されるために、浸炭焼入れは欠かせない技術です。
浸炭焼入れは、鋼材を 850℃~950℃ 程度まで加熱して、低炭素鋼材の表面に炭素を浸透させ、表層を硬化させる技術です。鋼材は炭素の含有量が増えるほど硬くなりますが、炭素量が多すぎると脆くなり、加工が難しくなります。このため、低炭素鋼に炭素を浸透させ、表面だけを硬化させることで、内部は柔軟で耐久性があり、表面は硬いという特性を持つ部品が作られます。これにより、機械部品は高い耐摩耗性と耐衝撃性を実現します。
浸炭焼入れには、固体浸炭、液体浸炭、ガス浸炭という3つの主要な方法がありますが、広く使われているのは、炭素を含むガス(メタンやプロパンなど)を炉内に送り込み、鋼材を加熱して炭素を浸透させるガス浸炭です。
浸炭焼入れの際、表面に浸透する炭素の量や深さは、温度や時間、炭素源の種類によって調整され、目的に応じた硬さや特性を持つ部品が作られます。浸炭焼入れは、浸炭 ⇒ 焼入れ ⇒ 洗浄 ⇒ 焼戻しという一連のプロセスで行われます。浸炭焼入れの深さは、一般的に0.2mmから3mm程度ですが、処理時間を延ばすことで、より深く浸透させることも可能です。また浸炭焼入れは、主に低炭素鋼や合金鋼などの金属部品において使用されます。
ガス浸炭におけるデメリット
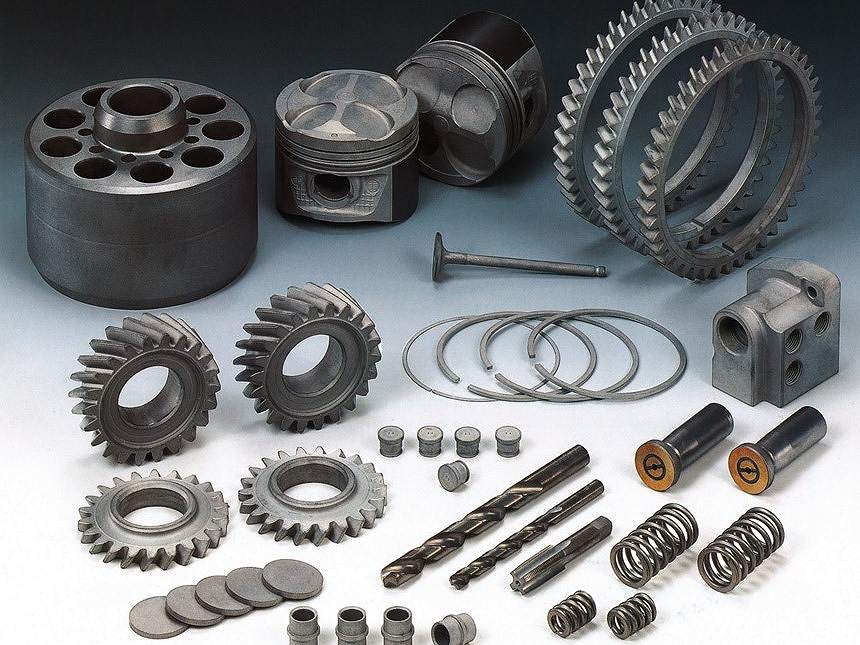
ガス浸炭は、従来から広く使われている熱処理技術の一つで、メタンやプロパンなどのガスを利用して鋼材に炭素を浸透させ、部品の表面を硬化させます。しかし、この方法にはいくつかのデメリットが存在し、特に近年では環境への配慮やコスト面から改善が求められています。
1. CO2排出量が多い
ガス浸炭では、浸炭プロセス中に大量のCO2を排出します。具体的には、ガス浸炭焼入れでは原料ガスとして、メタン、プロパンなどの炭化水素系ガスと空気を 1,050℃ 程度の変成炉中で触媒と反応させた変成ガス(一酸化炭素・水素・窒素)を用いて浸炭を行ないます。この浸炭焼入れの工程中で、原料ガスを不完全燃焼させて一酸化炭素(CO)を生成し、そのCOが鉄と化学反応を起こして浸炭を行います。この過程で、燃焼の副産物としてCO2が発生します。
特に、自動車部品や工業機械においては、24時間稼働する炉で長時間にわたり処理を行うため、CO2の排出量は非常に多くなります。これが、地球温暖化や環境負荷の原因となり、脱炭素化が求められる現代の製造現場において、大きな課題となっています。
2. エネルギー消費が大きい
ガス浸炭の炉は、一般的に高温で長時間稼働させる必要があるため、膨大なエネルギーを消費します。このエネルギーの大部分は、ガスを燃焼させるための燃料や、炉の運転に使用される電力です。24時間の連続運転が必要な炉も多く、エネルギーコストは大きくなる一方です。また、エネルギーの無駄遣いが環境負荷をさらに悪化させます。
3. 炉の安全性の課題
従来のガス浸炭炉では、燃焼による火災リスクが常に存在します。炉内では高温でガスを燃焼させているため、万が一設備トラブルが発生した場合、重大な事故に繋がる可能性があります。特に、長時間運転を行う現場では、定期的なメンテナンスや安全装置の設置が必須となりますが、それらもコスト増加の要因となります。
4. コストがかかる
ガス浸炭は、高温運転とガス供給による運転コストが高いだけでなく、設備のメンテナンスや、爆発等の事故を防ぐための安全対策に膨大な費用がかかります。さらに、CO2排出削減が求められる社会情勢の中で、これらの環境負荷に対する対策コストも無視できません。
5. 排気ガス処理の問題
ガス浸炭では、ガスの燃焼によって生じる排気ガスの処理が重要です。排気ガスにはCO2だけでなく、他の有害な化合物が含まれており、適切な処理をしなければ環境汚染の原因となります。このため、排ガス処理装置の導入や維持費も含めた総コストがかかってしまいます。
CO2をほとんど排出しない「常圧スマート浸炭」とは?
常圧スマート浸炭は、従来のガス浸炭に代わる革新的な浸炭技術で、CO2排出量を大幅に削減することが可能です。従来のガス浸炭では、メタンやプロパンなどの炭化水素系ガスを用いるため、多くのCO2が排出されていましたが、常圧スマート浸炭では、これらのガスを使用せずに処理を行うため、CO2発生原因となる変成炉を一切使用せず、環境負荷を大幅に軽減します。
常圧スマート浸炭の原理
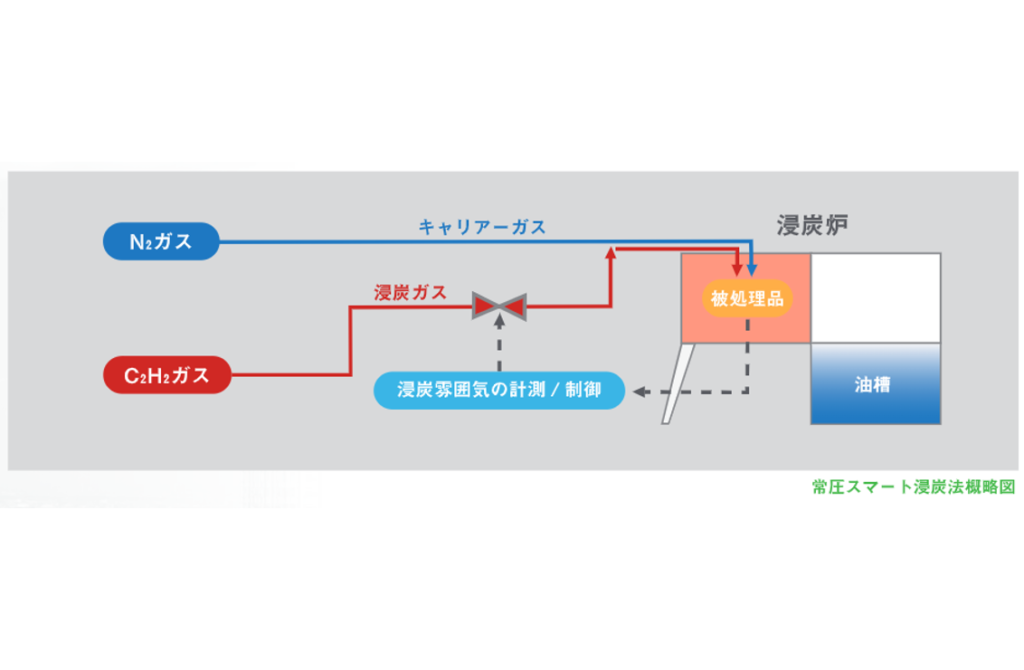
常圧スマート浸炭では、主にアセチレンガスと窒素ガスを使用します。アセチレンガスが鋼材の表面に炭素をダイレクトに供給し、窒素ガスがキャリアガスとして役割を果たします。
アセチレンガスは、非常に高い炭素濃度を持っているため、炭素供給源として機能し、効率的に表面硬化が可能であり、短時間で処理を終えることができます。またアセチレンは分解性が高く、制御が難しいガスですが、常圧スマート浸炭ではリアルタイムでアセチレン濃度を測定し、精密な制御を行うことで、効率的に炭素を浸透させることが可能です。これにより、エネルギー消費も抑えられ、さらにCO2の排出も大幅に削減されます。
また窒素ガスは、キャリアガスとしてアセチレンガスを運搬し、浸炭プロセス全体を安定させる役割を果たします。これにより、均一な炭素の浸透と表面硬化が実現します。
常圧スマート浸炭の特徴
常圧スマート浸炭は、従来のガス浸炭と真空浸炭のいいとこどりをした、CO2をほとんど排出しない画期的なガス浸炭方法です。常圧スマート浸炭は従来の浸炭技術と比較して、以下のような特徴があります。
1. CO2排出量の大幅削減
常圧スマート浸炭は、アセチレンガスを直接使用することで、従来のガス浸炭法に比べてCO2排出量を大幅に削減します。従来のガス浸炭では、可燃性雰囲気中で変成ガスを生成する過程で生じる大量のCO2が不要になるため、環境負荷を大幅に軽減できます。特に脱炭素化が求められるグローバル自動車メーカーやTier1メーカーの皆さまをはじめとした、カーボンニュートラルを目指す企業の方々が、この特徴から常圧スマート浸炭の導入検討を進められています。
2. 短時間での高効率処理
アセチレンガスの高い炭素供給効率により、浸炭時間が短縮されます。従来の浸炭プロセスでは、数時間から数日かかることもありましたが、常圧スマート浸炭では短時間で鋼材の表面に十分な炭素を浸透させることが可能です。このため、生産スピードが向上し、効率的な運用が可能になります。
3. 品質の均一性
常圧スマート浸炭は、ガスの流量や濃度をリアルタイムで制御するため、処理中の炭素の供給が安定しています。このため、表面硬化の均一性が向上し、製品全体にわたって一定の品質が保証されます。従来の浸炭法では、炭素の浸透が均一でない場合がありましたが、常圧スマート浸炭では、ばらつきが少なく安定した処理が可能です。
現場の安全性も改善する常圧スマート浸炭
常圧スマート浸炭は、従来のガス浸炭と比較して、現場の安全性を大幅に向上させる技術です。特に、燃焼ガスの管理や炉の運用に伴う火災リスクを大幅に軽減できる点が注目されています。
1. 火災リスクの軽減
従来のガス浸炭では、炉内で高温で燃焼ガス(メタンやプロパン)を使用するため、ガスの漏れや不適切な燃焼による火災リスクが常に存在していました。一方、常圧スマート浸炭では、変成ガスを使用せず、アセチレンガスを直接使用するため、ガスの燃焼プロセス自体が最小限に抑えられます。さらに、アセチレンガスはリアルタイムで濃度管理が行われるため、ガスの供給が過剰にならないように制御され、爆発等の火災事故リスクが低減されます。
2. 自動制御によるガス管理
常圧スマート浸炭では、ガスの供給と濃度がリアルタイムで自動制御されるシステムが導入されています。この制御システムは、アセチレンガスの濃度を常時モニタリングし、最適な量を鋼材に供給することで、効率的で安全な浸炭処理を実現します。この自動化により、従来必要だった人為的な操作ミスや、過剰なガス供給による危険性が大幅に低減されます。
3. 作業環境の改善
常圧スマート浸炭の導入により、作業現場でのガス漏れリスクや高温環境での作業負荷が大幅に軽減されます。従来のガス浸炭は、燃焼ガスの処理や高温管理が複雑で、また安全性の観点から24時間稼働を続ける必要があり、作業者に負担がかかる部分がありました。しかしこの新技術「常圧スマート浸炭」により、安全で快適な作業環境が提供され、作業者の熟練度を必要とせず、自動・無人稼働も可能になります。
日本テクノだからこそ可能な常圧スマート浸炭
常圧スマート浸炭は、日本テクノと高圧ガス工業が約8年前から共同研究を進めてきた技術です。この技術の開発は、アセチレンガスを使用し、従来のガス浸炭法と比べてCO2排出量をほぼゼロにできる環境対応型技術の確立を目指したものです。特に、炉内でのアセチレンガス濃度の計測と制御方法を確立したことにより、高品質かつ環境負荷の少ないガス浸炭が可能となりました。
日本政府は、「2050年カーボンニュートラル」を目指し、2030年度には2013年度比で温室効果ガスを46%削減する目標を掲げています。こうした背景のもと、熱処理分野においてもカーボンニュートラルに向けた製造プロセスの変革が求められています。常圧スマート浸炭は、これに対応するための技術として、エネルギー消費の削減とCO2排出量の大幅な低減を実現しました。
日本テクノだからこそ可能な常圧スマート浸炭の特徴は下記の通りです。
1. 既存設備の改造によるコスト削減&スムーズな導入
日本テクノでは、お客様の既存のガス浸炭炉を改造することで、常圧スマート浸炭を導入しています。この改造により、新規で常圧スマート浸炭炉や熱処理設備を導入する際と比較して、約1/3のコストで常圧スマート浸炭の導入が可能となります。特に、設備投資を抑えたい企業にとっては、大きなメリットとなります。また、改造後も既存の炉を使用し続けられるため、新たな設備導入による生産ラインの中断が最小限に抑えられます。
2. 徹底したサンプル実証と技術評価
日本テクノでは、既存炉の常圧スマート浸炭炉への改造の前に、当社の熱処理センターにてサンプル実証実験を行い、事前に品質確認を行います。お客様からサンプルを提供いただき、日本テクノの保有する常圧スマート浸炭炉で試作を行い、従来のガス浸炭と同等、もしくはそれ以上の品質を確認します。これにより、顧客は安心して技術導入を進めることができ、導入後のトラブルリスクも低減されます。
3. 幅広い業界での実績と信頼
日本テクノは、自動車部品、一般産業機械など、さまざまな業界で常圧スマート浸炭の実績を積んでいます。例えば、チェーン部品や歯車部品に対して常圧スマート浸炭を適用し、既存のガス浸炭と同等の品質を実現してきました。これらの豊富な実績が、同社の技術力と信頼性を裏付けています。
>>Go-Techナビ「次世代ガス浸炭法及び設備の開発により品質・生産性向上とコスト削減を実現」
常圧スマート浸炭の事例
ここでは、「熱処理技術ナビ」による常圧スマート浸炭の事例をご紹介します。現在は試作開発中の事例が多く、サイト上ではお見せできない事例の方が多くなりますので、予めご了承ください。
チェーンの常圧スマート浸炭 試作開発
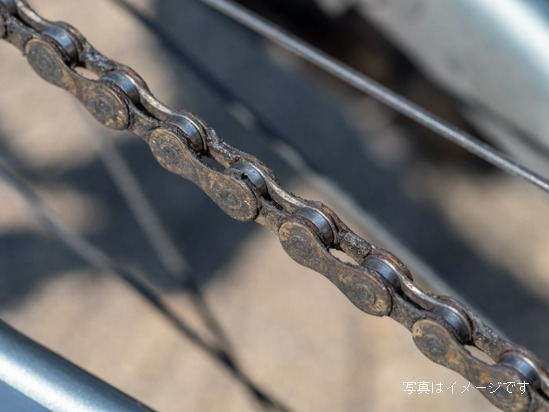
こちらはチェーン部品への常圧スマート浸炭の試作事例です。 お客様からは、「いまと同じ品質で、熱処理炉から火を消したい」というカーボンニュートラルを目的に、従来のガス雰囲気浸炭炉で実施している熱処理工程を、日本テクノの常圧スマート浸炭に置き換えることで脱炭素を推進できないかということで、試作のご相談いただきました。製品の規格や機能面はエンドユーザーとの関係もあり変更不可のため、同等品質のまま製造プロセスにおいて二酸化炭素の排出量を減らす必要がありました。 当社では、社内の熱処理加工センターにて常圧スマート浸炭の試作を行い、同等の品質で熱処理が行うことができているかの実証まで行っています。
歯車の常圧スマート浸炭 試作開発
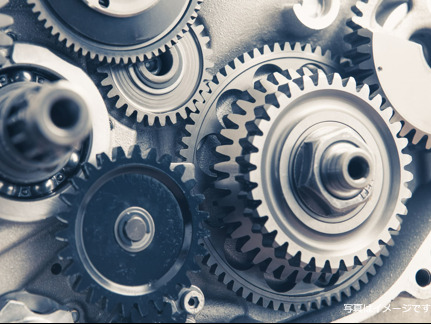
こちらは歯車への常圧スマート浸炭の試作事例です。 お客様からは、「いまと同じ品質で、熱処理炉から火を消したい」というカーボンニュートラルを目的に、従来のガス雰囲気浸炭炉で実施している熱処理工程を、日本テクノの常圧スマート浸炭に置き換えることで脱炭素を推進できないかということで、試作のご相談いただきました。製品の規格や機能面はエンドユーザーとの関係もあり変更不可のため、同等品質のまま製造プロセスにおいて二酸化炭素の排出量を減らす必要がありました。 当社では、社内の熱処理加工センターにて常圧スマート浸炭の試作を行い、同等の品質で熱処理が行うことができているかの実証まで行っています。
軸受けの常圧スマート浸炭 試作開発
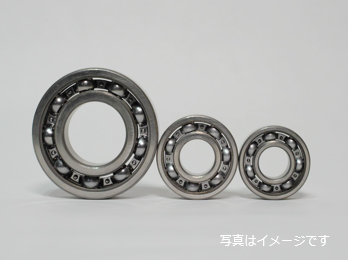
こちらは軸受け部品への常圧スマート浸炭の試作事例です。 お客様からは、「いまと同じ品質で、熱処理炉から火を消したい」というカーボンニュートラルを目的に、従来のガス雰囲気浸炭炉で実施している熱処理工程を、日本テクノの常圧スマート浸炭に置き換えることで脱炭素を推進できないかということで、試作のご相談いただきました。製品の規格や機能面はエンドユーザーとの関係もあり変更不可のため、同等品質のまま製造プロセスにおいて二酸化炭素の排出量を減らす必要がありました。 当社では、社内の熱処理加工センターにて常圧スマート浸炭の試作を行い、同等の品質で熱処理が行うことができているかの実証まで行っています。
「常圧スマート浸炭」カタログ
「熱処理技術ナビ」が提供する「常圧スマート浸炭」についてご紹介いたします。火を使わない、CO2をほとんど排出しない画期的な環境対応型のガス浸炭法です。
常圧スマート浸炭のことなら、「熱処理技術ナビ」にお任せください!
常圧スマート浸炭の技術相談については、「熱処理技術ナビ」にご相談ください。ご不明点や用途などお客様のご要望を考慮して、最適な技術提案をさせていただきます。
◇ 火のない熱処理工場・CO2が生まれない熱処理を実現
日本テクノが提供する熱処理加工や熱処理工場は、火がありません。当社のガス浸炭では火を使用しないため、天井には煤がなく、熱処理工場とは思えないくらい清潔感がある工場を維持することができます。
また、火を使わない熱処理工場では、燃焼が起こらないため、CO2ガスは発生しません。このCO2が出ない熱処理工場は、脱炭素社会に大きく貢献する地球に優しい熱処理技術として、日本国内の主要メーカーの方々からご相談をいただいております。
>>当社の特徴「いまだかつてない熱処理工場」について詳しくはこちら
ダイレクト浸炭については、下記動画でも解説しておりますでので、是非こちらを合わせてご覧ください!
このダイレクト浸炭の結果、ノズルの品質向上・長寿命化につながり、お客様から感謝のお声を頂くことができました。 熱処理技術ナビの「ダイレクト浸炭」では、アセチレンの反応性とパルス浸炭による細孔内部のガス交換により、部品全周に対して均一な浸炭を実現することができます。また当社は、ただ熱処理をするだけでなく、お客様のお困りごとを丁寧にお伺いした上で、課題を解決する熱処理方法を、使用するガスや制御機構段階からご提案いたします。
◇ 熱処理技術ナビの提供するサービス
熱処理技術ナビでは下記のサービスを展開しております。
◇対応可能な受託処理一覧
熱処理技術ナビを運営する株式会社日本テクノが対応可能な受託処理一覧をご紹介いたします!
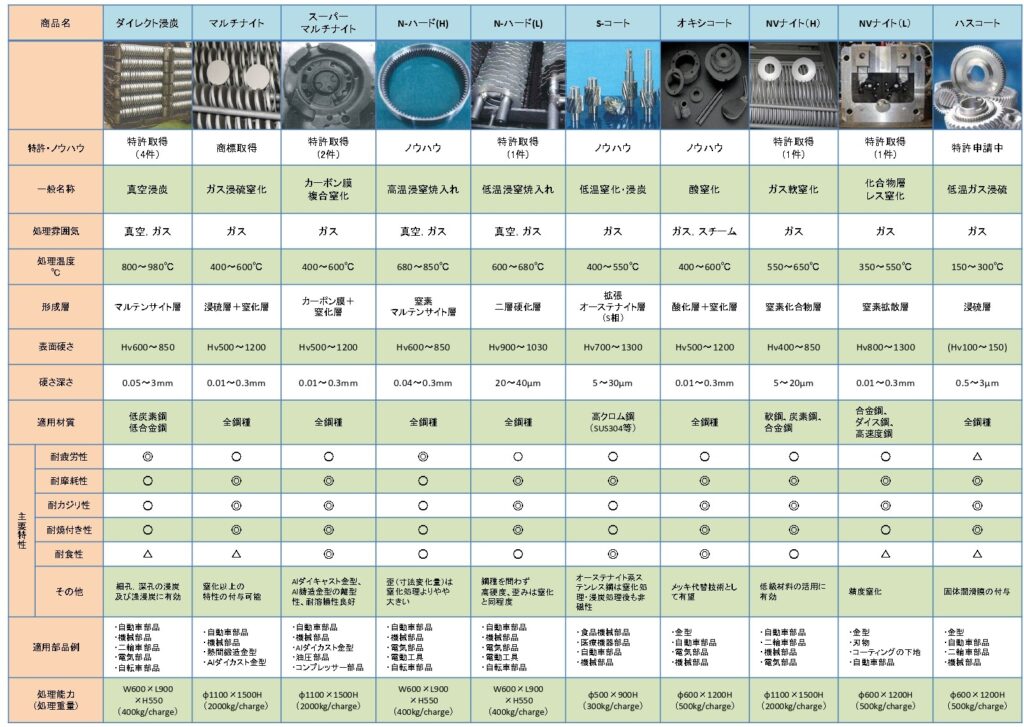
◇ お客様からいだくよくある質問
実際にお客様からいただいたご質問のうち、特によくいただく質問をご紹介します!
Q.ダイレクト浸炭では、どれくらいの深さまで浸炭焼入れできますか?
◇ 熱処理・炉のことでお困りの際は、熱処理技術ナビにお任せください!
熱処理・炉のことでお困りの際は、熱処理技術ナビにお気軽にご相談ください!
関連コラム
-
熱処理工程で脱炭素化する方法とは?CO2排出量0を実現する熱処理方法をご紹介
- 浸炭処理
- ダイレクト浸炭
2024/10/18
脱炭素社会を実現するためには、製造業、特に熱処理工程におけるCO2排出削減が重要な課題となっています。しかし従来のガス浸炭処理では、プロパンガスを燃焼させる過程で大量のCO2が発生しますが、新しい技術を取り入れることで、 […]... -
浸炭焼入れとは
- 浸炭処理
- ダイレクト浸炭
2024/03/26
浸炭焼入れの原理 浸炭焼入れは、鋼材の表面に炭素を浸透させて表面を硬化させる熱処理方法です。鋼材は炭素量が多いほど固くなりますが、多すぎると加工が難しくなります。そこで低炭素鋼に炭素を浸透させることで低炭素鋼に炭素を浸透 […]... -
ダイレクト浸炭とは
- 浸炭処理
- ダイレクト浸炭
2024/03/24
浸炭焼入れとは 浸炭焼入れは、鋼材の表面に炭素を浸透させて表面を硬化させる熱処理方法です。鋼材は炭素量が多いほど固くなりますが、多すぎると加工が難しくなります。そこで低炭素鋼に炭素を浸透させることで低炭素鋼に炭素を浸透さ […]...